Oil Rig: These behemoths of the sea are more than just metal and machinery; they represent a complex interplay of engineering, technology, and environmental responsibility. From the initial site survey to the eventual decommissioning, the life cycle of an oil rig is a fascinating journey, fraught with challenges and triumphs. This exploration delves into the various types of oil rigs, their operational processes, environmental impact, technological advancements, and the crucial aspect of responsible decommissioning.
We’ll uncover the intricacies of these offshore giants, examining their diverse structures, the skilled workforce that operates them, and the ever-evolving technologies shaping their future. We’ll also confront the environmental considerations inherent in oil extraction, exploring both the potential negative impacts and the mitigation strategies employed to minimize them.
Oil Rig Types and Structures
Oil rigs are complex structures designed for the extraction of oil and gas from beneath the seabed. Their design varies considerably depending on water depth, location, and the specific needs of the operation. Several key types exist, each with unique characteristics affecting their suitability for different environments and projects.
Oil rigs, those massive structures in the sea, require incredibly detailed planning. Think about the complex internal layouts – it’s almost like designing a small city! This is where tools like those mentioned in this article on AI home design tools that generate floor plans from images could be surprisingly useful. Imagine adapting that technology to optimize the space and workflow within an oil rig – a significant improvement in efficiency and safety could be achieved.
Ultimately, effective space planning is crucial for both oil rigs and houses alike.
Oil Rig Types
The choice of oil rig type depends heavily on water depth and the operational requirements. Three main types dominate the industry: jack-up rigs, semi-submersible rigs, and drillships. The following table summarizes their key differences:
Type | Water Depth Capability (meters) | Mobility | Cost (USD, approximate) |
---|---|---|---|
Jack-up Rig | Up to 150 | Relatively low; requires mobilization/demobilization | $50 million – $200 million |
Semi-submersible Rig | Up to 3000 | Moderate; can be towed to location | $200 million – $700 million |
Drillship | Up to 3000+ | High; self-propelled | $500 million – $1 billion+ |
Jack-up Rig Structural Components
A jack-up rig is characterized by its three or four legs that raise the platform above the water. This allows it to operate in relatively shallow waters. Here’s a text-based diagram illustrating its main components:“` Derrick | | | +—————–+—————–+ | | | | Platform | Platform | | | | +—————–+—————–+ | | | Leg | Leg | | | | | | ——–|—-|—-|——– | | | | | | | | | | | | | | | | | | | | | | | | | | | | | | | | | | | ——–|—-|—-|——– | | | | | | Leg | Leg | | Hull/Pontoons“`The diagram shows the derrick (the tall tower used for hoisting drilling equipment), the platform (the working area), the legs (which raise the platform above the water), and the hull or pontoons which provide buoyancy during transportation and positioning.
Materials Used in Oil Rig Construction
Oil rigs require robust materials capable of withstanding harsh marine environments and significant stress. Steel alloys are the most common material, chosen for their high strength-to-weight ratio and corrosion resistance. Specific alloys are selected based on the rig type and operating conditions. High-strength, low-alloy (HSLA) steels are frequently used for their superior yield strength and weldability. Concrete is also used, particularly in the construction of gravity-based platforms and the foundations of jack-up rigs, providing stability and buoyancy.
The selection of materials balances strength, durability, weight, and cost considerations.
Environmental Impact of Oil Rigs
Oil rigs, while crucial for energy production, have significant environmental consequences. Their impact extends beyond the immediate vicinity of the structure, affecting marine and atmospheric ecosystems on a larger scale. Understanding these impacts is critical for developing effective mitigation strategies and promoting sustainable energy practices.
Potential Environmental Impacts of Oil Rig Operations
The operation of oil rigs presents a range of environmental challenges. These impacts can be substantial and long-lasting, demanding careful consideration and proactive mitigation efforts.
Life on an oil rig is tough, demanding resilience and adaptability. Imagine designing your own perfect, relaxing home after a long shift – you can easily explore options with these affordable AI powered home design services available online , helping you plan your dream space. After a hard day’s work on the rig, a personalized, comfortable home is a welcome reward.
- Oil Spills: Accidental spills during drilling, transportation, or storage can devastate marine ecosystems. Oil coats wildlife, disrupting their ability to regulate body temperature, feed, and reproduce. The long-term effects include habitat destruction and population declines. The Deepwater Horizon oil spill in 2010 serves as a stark reminder of the catastrophic consequences of large-scale oil spills.
- Greenhouse Gas Emissions: The extraction, processing, and transportation of oil contribute significantly to greenhouse gas emissions, exacerbating climate change. Methane, a particularly potent greenhouse gas, is often released during oil extraction and can have a disproportionately large impact on global warming.
- Habitat Disruption: The construction and operation of oil rigs disrupt marine habitats. Noise pollution from drilling and rig activity can affect marine mammals’ communication and navigation. Physical alteration of the seabed during installation and removal can damage sensitive benthic communities. The presence of the rig itself can create a physical barrier, affecting marine life movement and breeding patterns.
Oil rigs, those massive structures in the sea, require incredibly detailed blueprints. Creating such complex designs benefits from advanced visualization, and that’s where technology like AI tools for creating realistic 3D models of home designs online comes into play. These tools could easily adapt to model the intricate piping and platforms of an oil rig, offering a far more efficient design process than traditional methods.
Ultimately, improving the design of oil rigs leads to safer and more productive operations.
- Wastewater Discharge: Oil rigs generate large volumes of wastewater containing chemicals, oil, and other pollutants. Discharge of this wastewater can contaminate marine environments, harming aquatic life and potentially affecting human health through the food chain. Improperly managed drilling muds can also lead to significant contamination.
- Air Emissions: Besides greenhouse gases, oil rig operations release other air pollutants, including volatile organic compounds (VOCs) and particulate matter. These pollutants can contribute to respiratory problems and other health issues in nearby communities.
Mitigation Methods for Environmental Impacts
Several strategies are employed to lessen the environmental footprint of oil rig operations. These range from preventative measures to post-incident cleanup and restoration efforts.
- Spill Prevention and Response: Implementing rigorous safety protocols, using advanced drilling technologies, and maintaining well-maintained equipment can significantly reduce the risk of oil spills. Furthermore, having comprehensive emergency response plans and readily available cleanup resources are essential for minimizing the impact of any spills that do occur.
- Waste Management Strategies: Effective waste management involves minimizing waste generation, recycling and reusing materials where possible, and safely disposing of hazardous waste. This includes responsible treatment and disposal of drilling muds, produced water, and other waste streams.
- Greenhouse Gas Reduction Technologies: Employing technologies to capture and store methane emissions, improving energy efficiency in rig operations, and exploring alternative energy sources for powering rigs can reduce the overall carbon footprint.
- Habitat Restoration and Mitigation: Implementing measures to minimize habitat disruption during construction and decommissioning, and undertaking restoration projects to rehabilitate damaged ecosystems, can help offset the negative impacts.
- Monitoring and Assessment: Regular monitoring of water and air quality, as well as marine life populations, allows for early detection of environmental problems and informs the development of more effective mitigation strategies.
Comparison of Environmental Impacts Across Oil Rig Types
The environmental impact varies depending on the type of oil rig. For instance, offshore platforms, due to their size and permanence, have a larger footprint than mobile rigs. Subsea wells, while potentially less visually intrusive, still present risks related to pipeline leaks and seabed disturbance. Jack-up rigs, because of their temporary nature, tend to have a smaller, though still significant, impact compared to fixed platforms.
Oil rigs, those massive structures in the sea, require incredibly detailed planning. Think about the complex internal layouts – it’s almost like designing a small city! This is where tools like those mentioned in this article on AI home design tools that generate floor plans from images could be surprisingly useful. Imagine adapting that technology to optimize the space and workflow within an oil rig – a significant improvement in efficiency and safety could be achieved.
Ultimately, effective space planning is crucial for both oil rigs and houses alike.
The specific environmental consequences are also influenced by factors such as location, water depth, and the type of oil being extracted. A thorough environmental impact assessment should be conducted for each specific project to evaluate the potential risks and develop tailored mitigation plans.
Technological Advancements in Oil Rig Technology
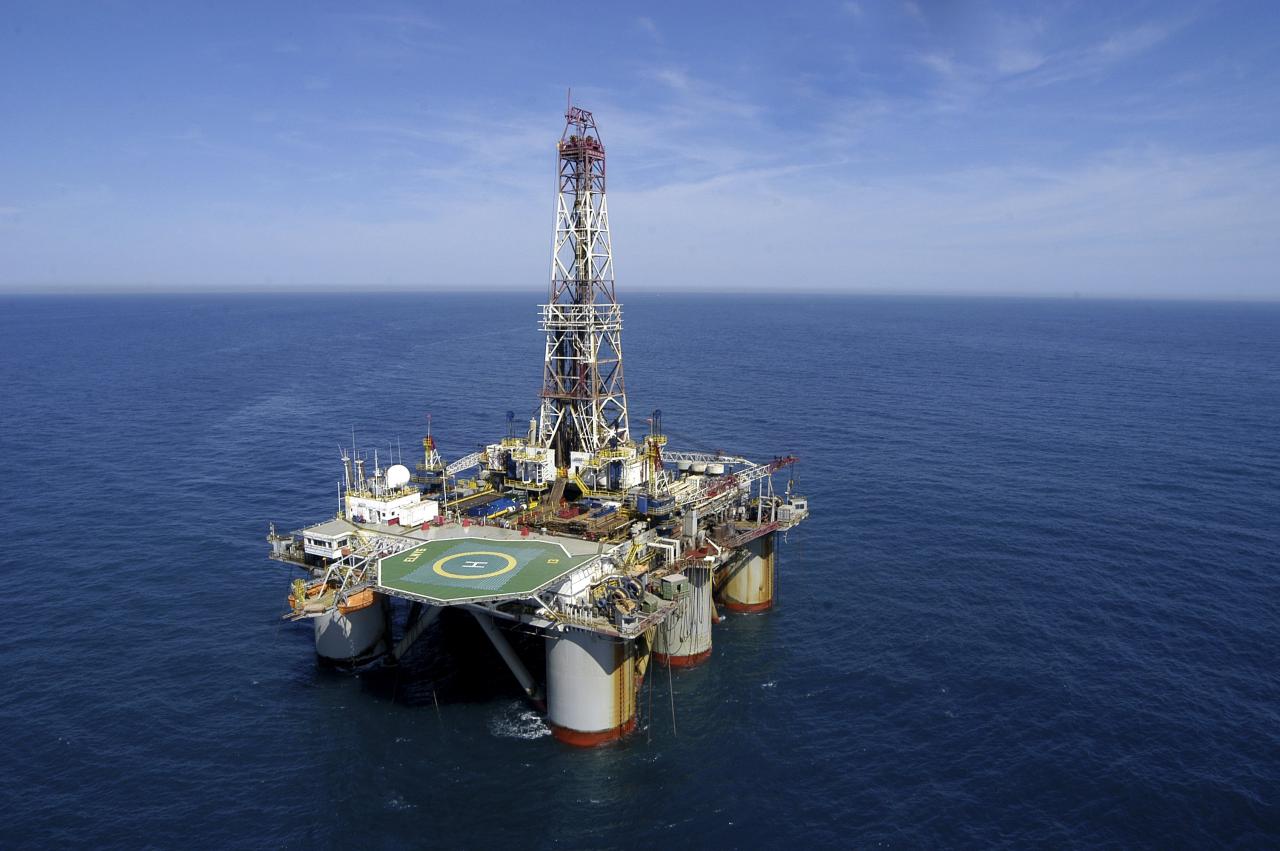
Source: rustpreservation.com
The oil and gas industry has witnessed significant technological advancements in recent decades, leading to improved efficiency, safety, and environmental performance in oil rig operations. These advancements encompass various aspects of drilling, production, and maintenance, contributing to a more sustainable and profitable industry.
Advancements in drilling technology have revolutionized oil extraction, making it possible to reach previously inaccessible reserves and operate in more challenging environments. Simultaneously, automation and robotics are transforming operations, enhancing safety and reducing human error. Furthermore, the industry is exploring and implementing renewable energy sources to minimize the environmental impact of oil rig operations.
Drilling Technology Advancements
Several key advancements in drilling technology have significantly improved efficiency and safety in oil rig operations. These improvements directly translate to cost savings and reduced environmental risks.
Oil rigs, those massive structures in the sea, require incredibly detailed blueprints. Creating such complex designs benefits from advanced visualization, and that’s where technology like AI tools for creating realistic 3D models of home designs online comes into play. These tools could easily adapt to model the intricate piping and platforms of an oil rig, offering a far more efficient design process than traditional methods.
Ultimately, improving the design of oil rigs leads to safer and more productive operations.
- Directional Drilling and Horizontal Drilling: These techniques allow for the drilling of wells at angles and horizontally, accessing reservoirs that were previously unreachable with traditional vertical drilling methods. This increases the amount of oil and gas that can be extracted from a single well, maximizing resource recovery.
- High-Pressure, High-Temperature (HPHT) Drilling: HPHT wells are located in extreme environments characterized by high temperatures and pressures. Advancements in drilling fluids, wellbore strengthening techniques, and specialized equipment have made accessing these challenging reservoirs safer and more efficient.
- Automated Drilling Systems: Real-time data acquisition and automated control systems have significantly improved the accuracy and speed of drilling operations. These systems monitor various parameters, providing immediate feedback and adjustments to optimize drilling performance and reduce the risk of accidents.
- Advanced Drilling Fluids: Improved drilling fluids, designed for specific reservoir conditions, enhance wellbore stability, reduce friction, and improve the efficiency of drilling operations. These fluids are often engineered to minimize environmental impact.
Automation and Robotics in Oil Rig Operations
The integration of automation and robotics is transforming oil rig operations, enhancing safety, improving efficiency, and reducing operational costs. These technologies handle tasks previously performed by humans in hazardous environments, minimizing risk and increasing productivity.
Imagine the cramped living quarters on an oil rig; even in such a harsh environment, people still crave comfort. Finding the right design to maximize limited space is key, which is why checking out resources like finding the best online AI tool for interior design projects could be helpful. Perhaps AI could even help design more efficient and aesthetically pleasing living spaces for future oil rig workers.
- Remotely Operated Vehicles (ROVs): ROVs are used for underwater inspections, maintenance, and repairs, eliminating the need for divers in hazardous subsea environments. They are equipped with cameras, manipulators, and various sensors to perform complex tasks remotely.
- Automated Drilling Systems: As mentioned previously, automated drilling systems optimize drilling parameters, enhancing efficiency and reducing human error. These systems continuously monitor wellbore conditions, adjusting drilling parameters in real-time to maintain optimal performance and safety.
- Robotics for Maintenance and Inspection: Robots are increasingly used for routine maintenance tasks, such as inspections of pipelines and equipment, reducing the need for human intervention in potentially dangerous areas. This minimizes human exposure to hazardous environments and increases the frequency of inspections.
- Autonomous Underwater Vehicles (AUVs): AUVs are used for subsea surveys and inspections, providing detailed information about the seabed and underwater infrastructure. They are capable of operating autonomously for extended periods, covering large areas efficiently.
Renewable Energy Integration in Oil Rigs
The oil and gas industry is actively exploring ways to reduce its carbon footprint. The integration of renewable energy sources into oil rig operations is a significant step towards achieving this goal. This reduces reliance on fossil fuels and decreases greenhouse gas emissions.
Oil rigs, those massive structures in the sea, require incredibly detailed blueprints. Creating such complex designs benefits from advanced visualization, and that’s where technology like AI tools for creating realistic 3D models of home designs online comes into play. These tools could easily adapt to model the intricate piping and platforms of an oil rig, offering a far more efficient design process than traditional methods.
Ultimately, improving the design of oil rigs leads to safer and more productive operations.
Conceptual Design for a Hybrid-Powered Oil Rig: A hybrid-powered oil rig could incorporate a combination of wind turbines, solar panels, and potentially wave energy converters to supplement the traditional power generation from fossil fuels. The renewable energy sources would be integrated into the rig’s power grid, providing a portion of the electricity needed for operations. A sophisticated energy management system would optimize the use of both renewable and traditional energy sources, ensuring a reliable and efficient power supply.
Excess renewable energy could even be stored in batteries for later use or potentially fed back into the grid.
Oil rigs, those massive structures in the sea, require incredibly detailed planning. The complexity rivals designing a home, so it’s helpful to know that there are amazing tools out there to help with the design process; check out best free online AI home design tools for beginners to get an idea of the software available. Applying similar design principles to smaller scales might help you better visualize the immense engineering feat that is an oil rig.
Oil Rig Decommissioning and Disposal
The end of an oil rig’s operational life necessitates a complex and costly process known as decommissioning. This involves the safe and environmentally responsible removal of the structure and its associated equipment, followed by the restoration of the surrounding marine environment. The process is heavily regulated and requires meticulous planning and execution to minimize environmental impact and ensure worker safety.
Decommissioning Stages
The decommissioning of an oil rig is a multi-stage process, often taking several years to complete. Each stage requires careful planning and execution to ensure safety and environmental protection.
- Planning and Assessment: This initial phase involves detailed surveys of the rig’s condition, environmental impact assessments, and the development of a comprehensive decommissioning plan. This plan must be submitted to and approved by relevant regulatory authorities.
- Equipment Removal: This stage involves the removal of all usable equipment, such as machinery, pipelines, and other valuable components. This equipment may be reused, refurbished, or sold for scrap.
- Platform Dismantling: Once the equipment is removed, the platform itself is dismantled. This often involves cutting the structure into smaller sections for easier transportation and disposal. Different techniques are employed depending on the size and type of the rig.
- Waste Management: All materials generated during the decommissioning process, including scrap metal, hazardous waste, and other debris, are carefully managed and disposed of according to environmental regulations.
- Site Restoration: The final stage involves restoring the seabed and surrounding environment to a condition that is as close as possible to its pre-installation state. This might involve filling in trenches, leveling the seabed, and replanting marine life.
Challenges and Costs of Decommissioning
Decommissioning oil rigs presents significant challenges and substantial financial burdens for operators.
- High Costs: The cost of decommissioning can be incredibly high, often running into hundreds of millions of dollars, depending on the size and complexity of the rig, its location, and the chosen decommissioning method. These costs are influenced by factors like labor, specialized equipment, transportation, waste disposal, and environmental remediation.
- Technological Challenges: Dismantling large, complex structures in harsh marine environments poses significant technological challenges. Specialized equipment and techniques are required, and the work must be carried out safely and efficiently.
- Environmental Regulations: Stringent environmental regulations must be adhered to throughout the decommissioning process, adding to the complexity and cost. These regulations vary depending on the location and the type of rig.
- Logistical Complexity: The logistical challenges of transporting large quantities of materials from remote offshore locations are substantial, adding further complexity and expense.
- Liability and Insurance: Operators face significant liability risks throughout the decommissioning process, requiring substantial insurance coverage.
Disposal Methods for Oil Rig Components
Several methods exist for disposing of oil rig components, each with its own advantages and disadvantages.
Disposal Method | Description | Advantages | Disadvantages |
---|---|---|---|
Recycling and Reuse | Salvaging usable components for reuse or recycling into other products. | Reduces waste, conserves resources, potentially generates revenue. | Not all components are recyclable; requires specialized facilities and processes. |
On-site Disposal | Leaving the rig in place, potentially after partial dismantling. | Potentially cheaper than removal, suitable for rigs in shallow waters. | Raises long-term environmental concerns; may not be permitted in all locations. |
Topside Removal and Disposal | Removing the topside structures and disposing of them onshore, leaving the jacket in place. | Reduces the amount of material requiring offshore disposal; allows for easier onshore recycling. | Still leaves a significant structure in the sea; requires specialized lifting and transport equipment. |
Complete Removal and Recycling | Complete removal of the entire structure for onshore recycling or disposal. | Minimizes long-term environmental impact; maximizes recycling potential. | Most expensive option; requires significant logistical planning and specialized equipment. |
Closure
From the imposing structures of jack-up rigs to the sophisticated technology powering drillships, the world of oil rigs is a dynamic blend of human ingenuity and natural resource extraction. Understanding their design, operation, and environmental impact is crucial, not only for ensuring safe and efficient oil production but also for mitigating the potential risks to our planet. As technology continues to advance, the future of oil rigs promises greater efficiency, reduced environmental impact, and improved safety protocols, shaping a more sustainable approach to offshore energy production.
Key Questions Answered: Oil Rig
What are the biggest risks associated with working on an oil rig?
The biggest risks include explosions, fires, falls from heights, and exposure to hazardous materials. Rigorous safety protocols are in place to mitigate these risks.
How long does it take to build an oil rig?
Construction time varies significantly depending on the rig type and complexity, ranging from several months to several years.
What happens to the oil extracted from an oil rig?
The extracted oil is typically transported via pipelines or tankers to refineries for processing into various petroleum products.
Are there any alternative energy sources being explored for powering oil rigs?
Yes, research is underway on using renewable sources like solar and wind power to supplement or replace traditional fossil fuel power sources on oil rigs, reducing their carbon footprint.