Horizontal Drilling revolutionized the energy industry, allowing access to previously unreachable resources. This technique, involving the drilling of wells horizontally after an initial vertical section, significantly increases the surface area of contact with underground reservoirs. This exploration into the world of horizontal drilling will cover its history, applications, techniques, challenges, and future prospects, offering a comprehensive understanding of this impactful technology.
From its humble beginnings to its current sophisticated applications in oil and gas extraction, geothermal energy, and even water resource management, horizontal drilling has consistently pushed the boundaries of what’s possible. We will delve into the intricacies of the process, exploring the specialized equipment, advanced drilling techniques, and environmental considerations involved. We’ll also examine the economic and environmental impacts, analyzing both the benefits and drawbacks of this powerful technology.
Definition and History of Horizontal Drilling
Horizontal drilling, a crucial technique in modern oil and gas extraction, involves drilling a wellbore that deviates significantly from a vertical path, eventually reaching a near-horizontal orientation. This allows access to vast reserves previously unreachable with traditional vertical drilling methods. The process requires sophisticated directional drilling technology and precise control to maintain the desired trajectory.
Horizontal drilling techniques have revolutionized oil extraction, allowing access to previously unreachable reserves. This is especially important when combined with methods like Enhanced Oil Recovery (EOR) , which boost production from mature fields. By extending the reach of wells, horizontal drilling maximizes the contact area with oil-bearing formations, ultimately improving the effectiveness of EOR techniques and overall oil production.
Fundamental Principles of Horizontal Drilling
Horizontal drilling relies on the principle of directional drilling, using specialized tools and techniques to steer the drill bit away from the vertical. This is achieved through a combination of mud motors, steerable downhole motors, and sophisticated measurement-while-drilling (MWD) and logging-while-drilling (LWD) systems. MWD tools provide real-time data on the wellbore’s position and orientation, allowing for continuous adjustments to maintain the desired trajectory.
LWD tools gather geological data about the formation, aiding in optimizing well placement and production. The process involves several stages, starting with a vertical section, followed by a build section where the wellbore is gradually curved, and finally a long horizontal section.
Historical Evolution of Horizontal Drilling Techniques
The concept of deviated drilling emerged in the early 20th century, primarily for accessing oil and gas deposits in challenging geological formations. Early attempts relied on simple techniques with limited control over the wellbore trajectory. However, the development of steerable downhole motors in the mid-20th century marked a significant milestone, enabling more precise control and longer horizontal sections.
The advent of MWD and LWD technologies in the latter half of the 20th century revolutionized the industry, allowing for real-time monitoring and adjustments, leading to significantly improved accuracy and efficiency. The integration of advanced technologies such as advanced drilling fluids, improved drill bit designs, and sophisticated modeling software further enhanced the capabilities of horizontal drilling.
Timeline of Advancements in Horizontal Drilling Technology
Year | Milestone | Impact |
---|---|---|
1920s-1930s | Early deviated drilling techniques using whipstocks | Limited directional control, short horizontal reaches |
1950s-1960s | Development of steerable downhole motors | Improved directional control, longer horizontal reaches |
1970s-1980s | Introduction of MWD and LWD technologies | Real-time monitoring and improved accuracy |
1990s-Present | Advanced drilling fluids, improved drill bit designs, sophisticated modeling software | Increased efficiency, longer horizontal reaches, improved well placement |
Comparison of Early and Modern Horizontal Drilling Methods
Feature | Early Methods | Modern Methods |
---|---|---|
Directional Control | Limited, reliant on whipstocks and other simple tools | Precise, using steerable downhole motors, MWD, and LWD |
Horizontal Reach | Short, often less than a kilometer | Extensive, often several kilometers |
Data Acquisition | Limited, often post-drilling surveys | Real-time data acquisition through MWD and LWD |
Efficiency | Lower, with higher chances of deviation errors | Higher, with reduced time and costs |
Applications of Horizontal Drilling
Horizontal drilling, once a niche technique, has revolutionized several industries, significantly impacting resource extraction and environmental management. Its ability to access previously unreachable resources and minimize surface impact makes it a valuable tool across various sectors. This section explores the key applications of this innovative drilling method.
Horizontal drilling is a specialized technique used to access hard-to-reach resources. It’s a significant advancement in the broader field of Drilling , allowing for more efficient extraction of oil, gas, and geothermal energy. This directional drilling method significantly increases the surface area accessible from a single wellbore, making it a crucial component of modern resource development.
The primary applications of horizontal drilling are widespread and impactful, influencing resource accessibility and efficiency in numerous ways. Its advantages, including increased wellbore contact with the reservoir and improved drainage, have driven its adoption across various sectors.
Oil and Gas Industry Applications
Horizontal drilling has become indispensable in the oil and gas industry, dramatically increasing hydrocarbon recovery rates. By extending the wellbore horizontally through a reservoir, it significantly increases the contact area with the producing formation. This leads to more efficient extraction of oil and natural gas, maximizing production and extending the life of the well. Furthermore, horizontal drilling allows for the targeting of multiple reservoir zones from a single wellbore, reducing the environmental footprint compared to multiple vertical wells.
Specific examples include enhanced oil recovery (EOR) techniques, where horizontal wells are used to inject fluids to improve the flow of oil, and shale gas extraction, where horizontal drilling combined with hydraulic fracturing has unlocked vast reserves of natural gas.
Geothermal Energy Extraction
Horizontal drilling plays a crucial role in geothermal energy development, particularly in Enhanced Geothermal Systems (EGS). Traditional geothermal power plants rely on naturally occurring fractures and high permeability in the subsurface. However, EGS utilizes horizontal drilling to create artificial fractures in hot, dry rock formations, thereby increasing permeability and allowing for the extraction of geothermal energy. The extended reach of horizontal wells enables access to larger volumes of hot rock, leading to increased power generation capacity.
For instance, projects like the Enhanced Geothermal Systems project in Basel, Switzerland, although encountering challenges, demonstrated the potential of this technology. While not without its difficulties, the potential for widespread adoption remains significant.
Water Resource Management Applications
Horizontal drilling techniques are increasingly employed in water resource management. Horizontal wells can be used for groundwater remediation, intercepting and extracting contaminated water for treatment. They can also be used for aquifer storage and recovery (ASR), where water is injected into aquifers during periods of low demand and withdrawn during peak demand. This method improves water security and helps manage water resources more efficiently.
Horizontal drilling is a game-changer in the energy industry, allowing access to previously unreachable resources. This technique is crucial for efficiently extracting hydrocarbons from challenging geological formations, especially when targeting significant deposits of Hydrocarbon Reserves. Ultimately, the widespread adoption of horizontal drilling has significantly boosted global oil and gas production.
Additionally, horizontal wells can be used for dewatering construction sites, minimizing the impact of groundwater on projects. A notable example is the use of horizontal wells for groundwater extraction in arid regions, maximizing water yield from limited resources.
Applications Summary
To summarize the diverse applications of horizontal drilling, here’s a concise overview across various industry sectors:
- Oil and Gas: Enhanced oil recovery, shale gas extraction, maximizing production from existing fields.
- Geothermal Energy: Enhanced Geothermal Systems (EGS), increasing permeability in hot, dry rock formations.
- Water Resource Management: Groundwater remediation, aquifer storage and recovery (ASR), dewatering.
- Other Sectors: Mineral exploration and extraction (e.g., coal bed methane), CO2 sequestration (potentially reducing carbon emissions).
Drilling Techniques and Equipment
Horizontal drilling requires specialized techniques and equipment to navigate the subsurface and create long, precisely placed wells. The process involves a complex interplay of advanced drilling technology and skilled personnel to overcome the challenges associated with directional drilling.
Drilling Techniques
Several techniques are employed during horizontal drilling operations to achieve the desired wellbore trajectory. These techniques are crucial for successfully reaching target formations and maximizing hydrocarbon recovery. The selection of a specific technique depends on factors such as the geological formations, the depth of the target reservoir, and the overall well design. Common techniques include rotary steerable systems (RSS), push-the-bit, and various types of directional drilling methods.
Horizontal drilling techniques are revolutionizing resource extraction, impacting everything from oil and gas to geothermal energy. Thinking about the broader environmental impact, efficient home design is crucial, and that’s where using online AI home design software that considers sustainability becomes important. Ultimately, minimizing environmental footprint, whether through resource extraction or construction, is key for a sustainable future, and horizontal drilling plays a role in both.
Rotary steerable systems, for example, allow for real-time adjustments to the wellbore path, providing greater control and precision. Push-the-bit techniques involve applying continuous force to the drill bit to maintain a specific direction, often used in conjunction with RSS for enhanced control.
Horizontal Drilling Rig Components
A horizontal drilling rig is a complex machine consisting of several key components working in concert. The efficiency and safety of the entire operation depend on the proper functioning of each part. Essential components include the drilling derrick, the top drive, the mud pumps, the drawworks, the rotary table, and the downhole assembly. The drilling derrick supports the entire drilling string and provides a framework for hoisting and lowering equipment.
The top drive rotates the drill string, allowing for precise control of the drilling process. Mud pumps circulate drilling fluid to lubricate the bit, remove cuttings, and control pressure within the wellbore. The drawworks is responsible for hoisting and lowering the drill string, while the rotary table (in older rigs) provides the rotational force to the drill string. The downhole assembly includes the drill string, drill bits, and various measurement-while-drilling (MWD) tools for real-time data acquisition.
Drilling Bits
Various types of drill bits are employed in horizontal drilling, each suited for specific geological formations and drilling conditions. The choice of bit depends on factors like rock hardness, formation abrasiveness, and the desired rate of penetration. Common types include roller cone bits, which use rotating cones with teeth to crush and cut rock, and polycrystalline diamond compact (PDC) bits, which utilize synthetic diamonds to cut rock.
Roller cone bits are generally more robust and effective in harder formations, while PDC bits are known for their longer lifespan and smoother cutting action, making them suitable for softer formations. The selection of the right bit directly impacts drilling efficiency, cost, and overall wellbore quality. For example, in shale formations, PDC bits are often preferred due to their ability to minimize formation damage.
Horizontal Wellbore Placement
[Diagram description: The diagram would depict a simplified, cross-sectional view of the Earth’s subsurface. It would show a vertical wellbore initially drilled, followed by a gradual curve into a horizontal section within the target reservoir. Arrows would indicate the direction of drilling. Key points such as the kick-off point (KOP), where the wellbore starts to deviate from vertical, and the build-up section, where the angle of inclination increases, would be clearly labeled.
Horizontal drilling, a technique used extensively in oil and gas extraction, requires significant upfront investment. Planning such projects often involves sophisticated modeling, and you might wonder about the cost of design tools; check out this article on how much does it cost to use online AI home design software for a related perspective on software costs.
Ultimately, the efficiency and accuracy of the initial design phase directly impact the overall cost and success of a horizontal drilling operation.
The horizontal section would be shown extending through the reservoir, with potential branches (laterals) possibly indicated. The target reservoir would be highlighted in a different color or shading to distinguish it from surrounding formations. Finally, the diagram would include a legend explaining the various components and labels.]
Challenges and Mitigation Strategies
Horizontal drilling, while offering significant advantages in resource extraction and infrastructure development, presents a unique set of challenges across environmental, technical, and safety domains. Addressing these challenges effectively is crucial for ensuring the responsible and sustainable application of this technology. Successful mitigation strategies require a multi-faceted approach combining technological innovation, robust regulatory frameworks, and diligent operational practices.
Environmental Challenges of Horizontal Drilling
Environmental concerns associated with horizontal drilling primarily revolve around potential impacts on water resources, air quality, and land ecosystems. These impacts can stem from the drilling process itself, the disposal of drilling fluids (muds), and potential leaks or spills of hydrocarbons. For instance, the contamination of groundwater aquifers through improperly managed waste disposal is a significant risk. Air emissions from drilling operations, including methane and other greenhouse gases, contribute to climate change.
Land disturbance caused by well pads and access roads can also lead to habitat fragmentation and erosion. Mitigation strategies involve implementing advanced waste management systems, utilizing environmentally friendly drilling fluids, employing leak detection and prevention technologies, and implementing rigorous environmental monitoring programs. Furthermore, responsible land reclamation practices are vital to minimizing the long-term ecological footprint of horizontal drilling operations.
Technical Challenges in Horizontal Drilling Operations
Achieving precise wellbore placement and maintaining directional control over extended horizontal sections present significant technical hurdles. The complexities increase with depth and the geological formations encountered. For example, encountering unexpected geological formations, such as fault zones or high-pressure zones, can lead to wellbore instability and potential loss of circulation. Furthermore, managing the friction and torque generated during drilling long horizontal sections requires sophisticated equipment and advanced drilling techniques.
Accurate formation evaluation and well completion are also critical to optimizing production. Mitigation strategies involve employing advanced drilling technologies, such as steerable drilling systems and real-time monitoring tools, to optimize wellbore placement and manage drilling parameters. Detailed geological modeling and pre-drilling site characterization are crucial to anticipate and mitigate potential geological challenges. Advanced well completion techniques, such as hydraulic fracturing, are employed to enhance hydrocarbon production from low-permeability formations.
Safety Precautions and Risk Mitigation Strategies
Safety is paramount in horizontal drilling operations, given the inherent risks associated with working in confined spaces, handling hazardous materials, and operating heavy machinery at significant depths. Potential hazards include blowouts, well control issues, equipment failures, and exposure to hazardous substances. Risk mitigation involves rigorous safety protocols, comprehensive training programs for personnel, and the implementation of advanced safety systems, including emergency shutdown systems and automated well control technologies.
Regular inspections and maintenance of equipment are critical to preventing failures. Emergency response plans must be in place to address potential incidents effectively and minimize their impact. Furthermore, the use of personal protective equipment (PPE) is mandatory to protect workers from potential hazards. The adoption of standardized operating procedures and a strong safety culture are essential to minimizing risks and ensuring the safety of personnel and the environment.
Successful Solutions to Common Horizontal Drilling Problems
Many challenges in horizontal drilling have been successfully addressed through technological advancements and improved operational practices. For example, the development of high-performance drilling fluids has significantly reduced the environmental impact of drilling waste and improved wellbore stability. Advanced wellbore imaging technologies allow for real-time monitoring of wellbore conditions, enabling proactive adjustments to drilling parameters and preventing potential problems. The implementation of automated drilling systems has improved efficiency and reduced the risk of human error.
Furthermore, the use of sophisticated modeling and simulation tools enables better planning and prediction of drilling challenges, leading to improved well design and execution. The successful completion of extremely long and complex horizontal wells in challenging geological settings demonstrates the effectiveness of these solutions. For instance, the development of extended-reach drilling techniques has enabled the extraction of hydrocarbons from previously inaccessible reservoirs.
Economic and Environmental Impacts
Horizontal drilling, while offering significant advancements in energy extraction, presents a complex interplay of economic benefits and environmental concerns. Understanding this duality is crucial for responsible resource management and policy development. The economic advantages are substantial, particularly in job creation and energy independence, but these must be weighed against potential risks to water resources, ecosystems, and air quality.
Economic Benefits of Horizontal Drilling
The economic benefits of horizontal drilling are widespread and significant. Increased oil and gas production leads to greater energy security for nations, reducing reliance on foreign imports and bolstering domestic economies. This increased production also translates into substantial revenue generation for governments through taxes and royalties. Furthermore, the industry itself creates numerous jobs, ranging from skilled drilling engineers and technicians to support roles in logistics and manufacturing.
The economic stimulus extends beyond the immediate industry, impacting related sectors like transportation and construction. For example, the Bakken shale formation in North Dakota saw a massive economic boom following the widespread adoption of horizontal drilling and hydraulic fracturing, creating tens of thousands of jobs and significantly increasing the state’s tax revenue. This economic impact, however, is not uniformly distributed and can lead to significant inequalities if not properly managed.
Horizontal drilling, a technique used extensively in oil and gas extraction, requires precise planning and complex modeling. Thinking about the intricate spatial considerations involved makes me wonder about the level of detail in comparing different AI powered home design platforms online ; do they offer similar capabilities for visualizing and manipulating 3D spaces? Ultimately, both horizontal drilling and home design benefit from advanced spatial reasoning and simulation tools.
Environmental Impacts of Horizontal Drilling
Horizontal drilling, particularly when coupled with hydraulic fracturing (“fracking”), carries potential environmental risks. The primary concern revolves around water contamination. Spills during drilling operations or leaks from improperly sealed wells can contaminate groundwater sources with drilling fluids, chemicals, and produced water. This contamination can have severe consequences for human health and ecosystems. Another major concern is the release of greenhouse gases (GHGs) such as methane, a potent GHG with a far greater warming potential than carbon dioxide.
Methane emissions during drilling, production, and transportation contribute to climate change. Finally, habitat disruption and fragmentation due to drilling activities can negatively impact wildlife and biodiversity. The extent of these impacts varies significantly depending on factors like the specific geology, drilling practices, and regulatory oversight. For example, inadequate well casing can lead to groundwater contamination, while insufficient methane capture systems can exacerbate climate change effects.
Comparison with Other Energy Extraction Methods
Compared to traditional vertical drilling, horizontal drilling generally yields higher energy production per well, reducing the overall land footprint required for a given energy output. However, the use of hydraulic fracturing, often associated with horizontal drilling, introduces additional environmental concerns not present in traditional methods. When compared to renewable energy sources like solar and wind, horizontal drilling has a considerably larger environmental impact due to GHG emissions and potential for water contamination.
Coal mining, on the other hand, often results in significantly greater land disturbance and air pollution, though the relative impact varies depending on specific mining techniques and environmental regulations. Nuclear power, while having a low carbon footprint, presents its own set of challenges related to radioactive waste disposal and potential accidents.
Summary of Economic and Environmental Pros and Cons
Aspect | Economic Pros | Economic Cons | Environmental Pros | Environmental Cons |
---|---|---|---|---|
Overall | Increased energy production, job creation, revenue generation for governments | Potential for economic boom-and-bust cycles, uneven distribution of economic benefits | Reduced land footprint compared to vertical drilling | Water contamination, GHG emissions, habitat disruption |
Specifics | Increased energy independence, stimulus to related industries | High initial investment costs, potential for price volatility | Potentially lower emissions than coal | Risk of methane leaks, potential for induced seismicity |
Future Trends and Innovations: Horizontal Drilling
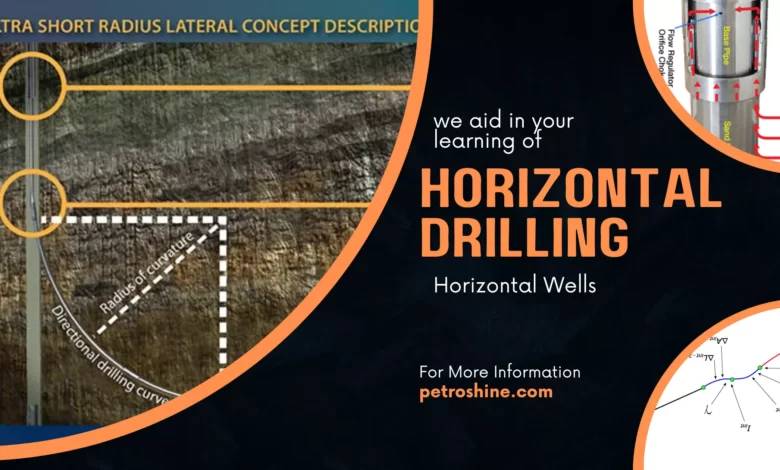
Source: petroshine.com
Horizontal drilling, a cornerstone of modern energy extraction and resource management, is poised for significant advancements driven by technological innovation and evolving industry needs. The future of this technology promises increased efficiency, reduced environmental impact, and expanded applications beyond traditional energy sectors.The next generation of horizontal drilling will be characterized by a convergence of advanced technologies, pushing the boundaries of what’s currently achievable.
This includes not only improvements in drilling equipment and techniques but also a significant shift towards automation and the integration of artificial intelligence (AI) for enhanced decision-making and operational optimization.
Emerging Technologies in Horizontal Drilling
Several emerging technologies are set to revolutionize horizontal drilling operations. These innovations aim to improve drilling speed, reduce costs, and enhance safety. For example, advancements in downhole drilling motors and rotary steerable systems (RSS) are allowing for greater precision and control during the drilling process, leading to more efficient wellbore placement and reduced non-productive time. Furthermore, the development of advanced drilling fluids, optimized for specific geological formations, minimizes friction and maximizes drilling efficiency.
The use of nanomaterials in drilling fluids is also being explored to enhance their properties and reduce environmental impact. Finally, the application of advanced sensors and real-time data analytics provides crucial insights into the drilling process, allowing for proactive adjustments and optimized well design.
Automation and Artificial Intelligence in Horizontal Drilling
Automation and AI are transforming horizontal drilling operations, moving towards autonomous drilling systems and predictive maintenance. Automated drilling systems can optimize drilling parameters in real-time, adapting to changing geological conditions and ensuring consistent performance. AI algorithms can analyze vast amounts of data from various sources – including sensors, geological models, and historical drilling data – to predict potential problems, optimize drilling parameters, and improve decision-making.
This leads to increased efficiency, reduced downtime, and improved safety. For instance, AI-powered systems can predict equipment failures before they occur, allowing for timely maintenance and preventing costly disruptions. Similarly, AI can optimize drilling trajectories to avoid geological hazards and maximize resource recovery. Companies like Schlumberger and Halliburton are already investing heavily in AI-driven solutions for the oil and gas industry, showcasing the significant potential of this technology.
Horizontal drilling is a game-changer in the energy industry, allowing access to previously unreachable reserves. This technique is especially vital for efficient Gas Exploration , as it maximizes the surface area contacted by the wellbore, ultimately extracting more natural gas. Because of its effectiveness, horizontal drilling continues to be a key technology for future gas production.
Future Research Directions in Horizontal Drilling Technology
Future research in horizontal drilling will focus on several key areas. One critical area is the development of more sustainable and environmentally friendly drilling fluids and practices. This includes research into biodegradable fluids and methods for minimizing waste generation. Another important research direction is the development of advanced sensors and data analytics techniques for improved real-time monitoring and control of drilling operations.
This could involve the development of new sensors capable of measuring a wider range of parameters with higher accuracy, as well as the development of advanced algorithms for data analysis and interpretation. Furthermore, research into improved drilling techniques for challenging geological formations, such as shale gas reservoirs, is crucial for expanding the applications of horizontal drilling. This includes exploring new drilling tools and techniques for navigating complex geological structures and maximizing resource extraction.
Finally, research into the integration of robotics and automation in horizontal drilling is essential for improving safety, efficiency, and productivity.
Predictions for the Future of Horizontal Drilling and its Impact on Energy Production
The future of horizontal drilling is bright, with significant potential to reshape energy production and resource management. We can expect to see a continued increase in the adoption of automation and AI, leading to more efficient and sustainable drilling operations. The development of new drilling technologies will enable the exploitation of previously inaccessible resources, potentially unlocking vast reserves of oil, gas, and geothermal energy.
This will have a significant impact on global energy security and the transition towards cleaner energy sources. For example, horizontal drilling is crucial for the development of geothermal energy, which is a clean and renewable energy source. Furthermore, advancements in horizontal drilling technologies are likely to reduce the environmental footprint of energy production by improving efficiency and reducing waste generation.
The integration of horizontal drilling with other technologies, such as carbon capture and storage, could further mitigate the environmental impact of fossil fuel extraction. While the precise timeline for these advancements is uncertain, the ongoing technological innovation and increasing demand for energy resources suggest a future where horizontal drilling plays an even more prominent role in meeting global energy needs.
Case Studies of Successful Horizontal Drilling Projects
Horizontal drilling has revolutionized the energy industry, enabling access to previously unreachable reserves and significantly increasing production efficiency. Examining successful projects highlights the innovative techniques and strategic planning required for optimal results. The following case studies illustrate the diverse applications and challenges overcome in various geographical and geological contexts.
Bakken Shale Formation, North Dakota
The Bakken Shale play in North Dakota represents a landmark achievement in horizontal drilling and hydraulic fracturing. This project involved drilling thousands of horizontal wells across a vast area, significantly increasing oil and gas production.
The Bakken formation presented several challenges, including the presence of thick shale layers with low permeability, requiring advanced fracturing techniques to stimulate production. Furthermore, the logistics of operating in a remote area, with limited infrastructure, posed significant operational hurdles. Solutions included deploying advanced drilling rigs capable of handling long horizontal reaches and employing sophisticated fracturing designs optimized for the specific geological characteristics of the Bakken shale.
The outcome was a dramatic increase in oil and gas production, transforming North Dakota into a major energy-producing state. This success spurred significant economic growth in the region, but also raised environmental concerns regarding water usage and wastewater disposal.
Offshore Oil and Gas Exploration in the Gulf of Mexico
Horizontal drilling has enabled the exploitation of offshore oil and gas reserves in deepwater environments, previously considered too challenging to access. The development of the Perdido field in the Gulf of Mexico exemplifies this achievement.
Drilling in deepwater environments presents unique challenges, including high pressure and temperature conditions, the risk of wellbore instability, and the logistical complexities of operating in a remote marine setting. Solutions involved the use of advanced drilling technology, including dynamic positioning systems for drilling rigs, sophisticated wellbore monitoring systems, and specialized drilling fluids to maintain wellbore stability. The Perdido field development demonstrated the feasibility of extending horizontal drilling into ultra-deepwater environments, significantly expanding the potential for offshore oil and gas production.
However, the high cost of development and the environmental risks associated with offshore drilling remain significant considerations.
Tight Gas Reservoirs in the Marcellus Shale, Pennsylvania
The Marcellus Shale, located in the Appalachian Basin, is another prime example of the successful application of horizontal drilling and hydraulic fracturing in unconventional gas reservoirs.
The Marcellus Shale, characterized by its low permeability and high pressure, presented challenges in terms of wellbore stability and efficient gas production. Solutions included the use of high-strength steel casing, advanced drilling fluids, and optimized hydraulic fracturing designs tailored to the specific geological characteristics of the Marcellus shale. The outcome was a significant increase in natural gas production, contributing to a shift in the North American energy landscape.
Horizontal drilling is a game-changer in oil and gas extraction, allowing access to previously unreachable resources. This technique is especially effective when targeting extensive reservoirs, like those described on this informative website about Reservoir characteristics. By drilling horizontally through the reservoir, companies can significantly increase the contact area with the resource, leading to greater production efficiency.
The development of horizontal drilling has revolutionized how we tap into underground resources.
However, the environmental impact of hydraulic fracturing in the Marcellus Shale, particularly regarding water contamination and induced seismicity, has been a subject of considerable debate and regulatory scrutiny. This case study highlights the need for responsible environmental management alongside technological advancements.
Illustrative Examples of Horizontal Well Paths
Horizontal drilling allows for significantly increased contact with the reservoir, leading to higher production rates compared to vertical wells. The path a horizontal well takes, however, is carefully planned and depends on several geological and operational factors. Different wellbore trajectories are employed to optimize reservoir drainage and maximize hydrocarbon recovery.Different wellbore trajectories are designed to efficiently access and exploit hydrocarbon reservoirs.
The design process considers factors such as reservoir geometry, fault lines, and the presence of impermeable layers. The goal is to maximize the well’s contact with the productive zones while minimizing drilling risks and costs.
S-Shaped and J-Shaped Wellbore Trajectories
The S-shaped trajectory involves an initial vertical section, followed by a build section to reach the target reservoir, then a horizontal section extending through the reservoir, and finally a gradual curve back towards the surface. This design is particularly useful in reservoirs with complex geological structures or where multiple layers need to be accessed. The J-shaped trajectory is simpler, featuring a vertical section followed by a build section directly into the horizontal section within the reservoir.
This is often preferred for simpler reservoir geometries and reduces drilling time and complexity. The choice between these designs depends on the specific geological characteristics of the reservoir.
Factors Influencing Wellbore Trajectory Design
Several factors influence the design of a horizontal well’s trajectory. Reservoir characteristics, including the thickness, extent, and permeability of the productive zones, are primary considerations. The presence of faults, fractures, and other geological features dictates the path to avoid complications or to optimally intersect productive zones. Operational constraints, such as the available drilling equipment and the maximum allowable wellbore inclination, also play a crucial role.
Finally, the presence of sensitive environmental zones may necessitate modifications to the trajectory to minimize environmental impact.
Geological Formations Encountered During Horizontal Drilling
Horizontal drilling often encounters a variety of geological formations, each with unique properties that affect drilling operations. These formations can include sedimentary rocks like sandstones, shales, and limestones, as well as igneous and metamorphic rocks depending on the location. Sandstones, often highly permeable and porous, are prime targets for hydrocarbon extraction. Shales, known for their low permeability, can present challenges due to the potential for wellbore instability and formation fracturing.
Limestones, depending on their characteristics, can offer excellent reservoir properties or pose difficulties during drilling. Understanding the specific geological formations encountered is crucial for optimizing drilling parameters and minimizing risks.
Cross-Section of a Horizontal Well in a Reservoir
Imagine a cross-section of a reservoir showing multiple layers. A horizontal well, depicted as a long, relatively straight line, extends through the most productive layer of the reservoir. Above and below this productive zone, other layers are visible, some possibly containing less productive zones or impermeable formations like shale. The wellbore itself is surrounded by the reservoir rock.
The well’s casing, a protective steel pipe, is clearly visible, extending from the surface down to the horizontal section. Branching from the main horizontal wellbore might be smaller, shorter laterals extending into other parts of the reservoir to enhance its drainage. The illustration highlights the increased contact area the horizontal well achieves compared to a vertical well, leading to greater hydrocarbon recovery.
Summary
Horizontal drilling has undeniably transformed the energy landscape, offering a pathway to efficient resource extraction and sustainable energy solutions. While challenges remain, ongoing innovations and advancements in technology continue to mitigate risks and improve efficiency. The future of horizontal drilling is bright, promising further advancements in automation, artificial intelligence, and environmentally responsible practices, ensuring its continued role in shaping our energy future.
The detailed exploration provided here serves as a strong foundation for understanding this complex and critical technology.
General Inquiries
What are the main environmental risks associated with horizontal drilling?
Potential risks include groundwater contamination, methane emissions, and habitat disruption. Mitigation strategies are crucial to minimize these impacts.
How does horizontal drilling compare to vertical drilling in terms of efficiency?
Horizontal drilling generally yields significantly higher production rates from reservoirs due to the increased contact area, making it more efficient in extracting resources.
What is the role of automation in modern horizontal drilling?
Automation enhances safety, precision, and efficiency by reducing human error and optimizing drilling parameters in real-time.
What are some examples of emerging technologies in horizontal drilling?
Examples include advanced drilling fluids, improved downhole tools, and the use of data analytics for predictive maintenance and optimized well placement.