Drilling, a seemingly simple act of making holes, underpins a surprisingly diverse range of industries. From extracting oil and gas from deep beneath the ocean’s surface to performing intricate medical procedures and exploring the Earth’s geological secrets, drilling technologies are essential. This exploration will delve into the multifaceted world of drilling, examining its various applications, the challenges it presents, and the innovative technologies shaping its future.
We’ll uncover the fascinating techniques and safety protocols employed across different sectors, from the massive machinery used in oil extraction to the precision instruments utilized in microsurgery.
We’ll cover the different types of drilling equipment, from the colossal rigs used in offshore oil exploration to the smaller, more precise drills used in construction and medical settings. We’ll also explore the environmental impact of drilling and the measures taken to mitigate its effects, highlighting the importance of sustainable practices. The journey will cover everything from the historical methods to the latest advancements in automation and data analytics, showcasing how drilling has evolved and continues to evolve.
Drilling in the Oil and Gas Industry
Drilling for oil and gas is a complex and crucial process underpinning the global energy supply. It involves a range of technologies and techniques, each adapted to specific geological conditions and operational environments. The efficiency and safety of drilling operations are paramount, demanding meticulous planning and execution.
Drilling for plumbing or electrical work can be a hassle, especially if you’re not sure where things are located. Planning your home’s layout beforehand is key, which is why using AI powered home design software that integrates with smart home tech can be a game-changer. This helps you visualize the location of pipes and wires before you even pick up a drill, preventing costly mistakes.
Types of Drilling Rigs
Different drilling rigs are employed depending on the location and type of well. The choice considers factors like water depth, terrain, and the anticipated well trajectory.
Drilling down into the details of a project can be time-consuming, but finding the right tools can make all the difference. If you’re working on an interior design project, consider checking out this helpful guide on finding the best online AI tool for interior design projects to streamline your workflow. Ultimately, efficient tools, like the right AI, are crucial for precise and effective drilling down to the core of any design challenge.
Rig Type | Capabilities | Applications | Advantages |
---|---|---|---|
Land Rig | Drilling on land, varying sizes and capabilities depending on well depth and complexity. | Onshore oil and gas wells, typically in accessible locations. | Relatively lower initial investment compared to offshore rigs; easier access for maintenance and personnel. |
Jack-up Rig | Elevates above water using legs, suitable for shallow water depths. | Offshore oil and gas wells in shallow waters. | Stable platform in moderate sea conditions; relatively cost-effective for shallow water drilling. |
Semi-submersible Rig | Floats on pontoons, providing stability in deeper waters. | Offshore oil and gas wells in moderate water depths. | Greater stability than jack-ups in rougher seas; capable of operating in deeper waters. |
Drill Ship | Dynamic positioning system maintains position; capable of operating in very deep waters. | Offshore oil and gas wells in deep and ultra-deep waters. | Operates in the deepest waters; high mobility. |
Steps Involved in Drilling an Oil or Gas Well
The drilling process follows a systematic sequence of steps to ensure efficiency and safety. Variations exist depending on the specific well design and conditions.
- Site Preparation: This includes surveying the land, constructing access roads, and setting up the drilling rig.
- Spudding: The initial penetration of the earth’s surface to begin the wellbore.
- Drilling the Wellbore: Using a drill bit, progressively drilling deeper into the earth, removing cuttings with drilling mud.
- Casing and Cementing: Installing steel casing to stabilize the wellbore and protect against collapse; cementing the casing to seal the annulus.
- Formation Evaluation: Testing the formation to determine the presence and properties of hydrocarbons.
- Completion: Preparing the well for production by installing perforations, screens, and other equipment.
- Production Testing: Testing the well’s productivity to assess the flow rates and hydrocarbon composition.
Challenges of Offshore Drilling and Mitigation Strategies
Offshore drilling presents unique challenges compared to land-based operations. These challenges necessitate robust safety measures and advanced technologies.
Drilling into a project can be tough, especially when visualizing the final result. Luckily, planning is easier now thanks to online AI home design software with 3D rendering capabilities , which lets you see your design in 3D before you even pick up a drill. This helps you avoid costly mistakes and refine your drilling plans for a smoother, more accurate process.
- Harsh Weather Conditions: Strong winds, waves, and currents can disrupt operations and damage equipment. Mitigation involves advanced weather forecasting, robust rig design, and the ability to quickly secure the rig in case of severe weather.
- Deepwater Operations: The extreme pressures and temperatures at great depths pose significant engineering challenges. Mitigation involves specialized equipment and materials designed to withstand high pressure and temperature, as well as advanced remote-operated vehicles (ROVs) for underwater inspections and repairs.
- Environmental Risks: Oil spills and other environmental incidents can have devastating consequences. Mitigation includes stringent safety protocols, emergency response plans, and the use of advanced spill containment technologies.
- Logistical Challenges: The remote location of offshore rigs requires careful planning and coordination of logistics. Mitigation involves efficient supply chain management, advanced communication systems, and the use of specialized vessels for transportation.
Directional Drilling vs. Horizontal Drilling
Directional and horizontal drilling techniques are used to access reservoirs that are not directly beneath the drilling location.
- Directional Drilling: Involves deviating from a vertical path to reach a target reservoir at an angle. This is often used to access multiple reservoirs from a single wellbore or to avoid obstacles.
- Horizontal Drilling: A type of directional drilling where the wellbore is drilled horizontally for an extended distance within the reservoir. This maximizes contact with the producing formation, increasing production efficiency.
Drilling in the Construction Industry
Drilling plays a vital role in various construction projects, from creating holes for anchoring to excavating foundations. The choice of drilling equipment depends heavily on the specific application, the material being drilled, and the scale of the project. Different drills offer varying levels of power, precision, and versatility. Understanding these differences and implementing proper safety measures are crucial for successful and safe construction projects.
Types of Drills Used in Construction and Their Applications
The selection of the appropriate drill for a construction task is paramount to efficiency and safety. Incorrect drill selection can lead to damage to materials, equipment failure, and potential injury. Here’s a breakdown of common drill types and their uses:
- Hammer Drills: These drills use a hammering action in conjunction with rotation, making them ideal for drilling into concrete, brick, and stone. Their impact force allows them to penetrate hard materials more effectively than standard rotary drills.
- Rotary Drills: These drills use only rotational force, making them suitable for softer materials like wood, metal, and plastics. They are often used for smaller-scale tasks and offer greater precision than hammer drills.
- Core Drills: These drills extract cylindrical cores of material, typically used for obtaining samples or creating precise openings in concrete, masonry, or asphalt. They are often used for plumbing or electrical installations needing large, clean holes.
- Auger Drills: These drills use a screw-like bit to bore holes in the ground, typically used for creating holes for posts, pilings, or other foundation elements. They are commonly seen in large-scale earthworks.
- Diamond Core Drills: These drills utilize diamond-tipped bits to cut through extremely hard materials like reinforced concrete or granite with exceptional precision. They are frequently employed for specialized applications such as creating openings for large pipes or ventilation systems.
Safety Precautions for Drilling Equipment in Construction
Operating drilling equipment requires strict adherence to safety protocols to prevent accidents and injuries. These precautions vary depending on the type of drill being used but generally encompass several key areas:
- Personal Protective Equipment (PPE): Always wear safety glasses, hearing protection, and appropriate gloves. For larger drills, a hard hat and dust mask may also be necessary.
- Secure Work Area: Ensure the work area is clear of obstructions and that the drill is stable and properly secured before operation. Use appropriate clamps or stands where needed.
- Correct Drill Selection: Choose the appropriate drill bit for the material being drilled to prevent damage to the equipment or material and to avoid kickback.
- Proper Technique: Use the correct drilling technique for the specific drill type. Avoid excessive force, which can lead to equipment failure or injury.
- Regular Maintenance: Regularly inspect and maintain drilling equipment to ensure it’s in good working order. Replace worn or damaged parts immediately.
- Emergency Procedures: Be aware of emergency procedures and have a plan in place in case of an accident or equipment malfunction.
Drilling Operation Safety Checklist
A comprehensive safety checklist is crucial for minimizing risks associated with drilling operations. This checklist should be reviewed and signed off before commencing any drilling work.
Item | Check |
---|---|
PPE worn correctly | ☐ |
Work area clear of obstructions | ☐ |
Drill properly secured | ☐ |
Correct drill bit selected | ☐ |
Emergency procedures understood | ☐ |
Equipment inspected and maintained | ☐ |
Proper ventilation in place (if necessary) | ☐ |
Best Practices for Managing Drilling-Related Waste
Drilling operations often generate waste materials, including dust, debris, and broken drill bits. Proper waste management is crucial for environmental protection and worker safety.
- Waste Segregation: Separate different types of waste materials (e.g., concrete dust, metal shavings) for proper disposal.
- Dust Control: Use appropriate dust control measures, such as vacuum systems or water sprays, to minimize dust generation and airborne particulate matter.
- Proper Disposal: Dispose of waste materials according to local regulations and environmental guidelines. Many construction waste materials can be recycled or reused.
- Spill Response Plan: Have a plan in place to address any spills of hazardous materials that may occur during drilling operations.
Drilling in the Medical Field
Medical drilling, while seemingly a niche application, plays a crucial role in various surgical procedures, impacting patient outcomes significantly. From creating precise bone access points to preparing sites for implants, the accuracy and control offered by medical drilling tools are paramount. This section explores the diverse applications of drilling in medicine, safety protocols, and the evolution towards minimally invasive techniques.
Types of Medical Drilling Procedures and Their Applications
Medical drilling encompasses a range of procedures tailored to specific anatomical locations and surgical objectives. The precision and control required demand specialized equipment and techniques. The table below illustrates some common examples.
Procedure Type | Application | Drill Type | Benefits |
---|---|---|---|
Craniotomy | Surgical access to the brain | High-speed, low-torque drills with specialized bits | Minimally invasive approach, reduced trauma |
Orthopedic Surgery (e.g., joint replacement) | Preparing bone for implants, creating fixation points | Variable-speed drills with different bit sizes and shapes | Precise bone preparation, secure implant placement |
Dental Procedures | Preparing tooth structure for fillings, crowns, or implants | High-speed handpieces with various burs | Precise cavity preparation, minimal tooth removal |
ENT Surgery | Creating access points in the skull base or sinuses | Microsurgical drills with fine-tipped bits | Precise drilling in delicate areas, reduced risk of damage |
Safety Protocols and Sterilization Procedures for Medical Drilling Equipment
Maintaining sterility and ensuring patient safety are paramount in medical drilling. Strict adherence to sterilization protocols is essential to prevent infections. All drilling equipment, including handpieces, bits, and associated instruments, must undergo rigorous sterilization before, during, and after each procedure. This typically involves autoclaving (high-pressure steam sterilization) or other validated sterilization methods. Pre-operative checks of equipment functionality and meticulous handling techniques by trained surgical personnel are critical aspects of safety.
The use of appropriate personal protective equipment (PPE), such as gloves, masks, and eye protection, further minimizes the risk of contamination and injury to both the patient and the surgical team. Regular maintenance and calibration of drilling equipment are also crucial for ensuring optimal performance and minimizing the risk of malfunctions.
Drilling down into the specifics of a home renovation project can be overwhelming. But planning gets easier when you utilize the intuitive tools found on top rated AI home design websites with easy user interfaces to visualize your ideas. These sites can help you plan the precise placement of everything, from plumbing to electrical work, making the actual drilling process much more efficient and accurate.
Minimally Invasive Drilling Techniques Used in Modern Surgery
Minimally invasive surgical techniques have revolutionized medical drilling, resulting in smaller incisions, reduced trauma, faster recovery times, and improved cosmetic outcomes. These techniques often employ smaller diameter drills, specialized instrumentation (e.g., robotic-assisted surgery), and advanced imaging technologies (e.g., intraoperative fluoroscopy) to guide the drill with high precision. Computer-assisted surgery, for example, allows for pre-operative planning and real-time tracking of the drill’s position during the procedure, enhancing accuracy and minimizing the risk of unintended damage to surrounding tissues.
Comparison of Traditional and Minimally Invasive Surgical Drilling Techniques
Traditional surgical drilling often involved larger incisions, leading to greater tissue trauma, longer recovery times, and increased risk of complications. Minimally invasive techniques, in contrast, prioritize smaller incisions, reduced tissue damage, and shorter hospital stays. While minimally invasive techniques offer significant advantages, they may require specialized training, more advanced equipment, and may not be suitable for all procedures.
Drilling is crucial for various construction projects, from laying foundations to installing utilities. Before you start drilling though, you might want to finalize your home design using AI; check out this helpful guide on how to use AI to design my dream home online for free to ensure accurate placement of features. Once you have your perfect blueprint, you can confidently proceed with the drilling phase, knowing exactly where everything needs to go.
The choice between traditional and minimally invasive approaches depends on several factors, including the patient’s condition, the specific surgical requirements, and the surgeon’s expertise.
Drilling in Geological Research
Geological drilling plays a crucial role in understanding the Earth’s subsurface, providing invaluable data for resource exploration, environmental assessment, and scientific research. This process allows geologists to directly sample and analyze rock formations, providing insights unavailable through surface observations alone.
Core Drilling Methods for Geological Exploration
Core drilling involves extracting cylindrical samples of rock, known as cores, from the subsurface. Several methods exist, each suited to different geological conditions and project requirements. Diamond core drilling, for instance, uses a diamond-encrusted drill bit to cut through hard rock formations, producing high-quality cores with minimal disturbance. Percussion drilling, on the other hand, uses a hammering action to break up rock, which is then collected in segments.
Drilling is crucial for many home improvement projects, from installing shelves to creating intricate designs. When planning a major renovation, however, you might find it helpful to visualize the entire project beforehand using online tools. Check out this resource for comparing different AI powered home design platforms online to aid your planning. This can help you optimize your drilling locations and avoid costly mistakes, ensuring a smoother, more efficient drilling process in the end.
The choice of method depends on factors such as rock hardness, depth of investigation, and the desired core quality. Rotary drilling techniques utilize rotating drill bits to extract cores and are frequently used in softer rock formations.
Geological Model Creation Using Drilling Data
Drilling data, encompassing core samples, borehole logs (records of the drilling process), and geophysical logs (measurements of physical properties of the subsurface), are essential for creating accurate geological models. Geologists analyze this data to interpret the subsurface stratigraphy (layer arrangement), lithology (rock types), and structural features (faults, folds). This information is then integrated into three-dimensional models using specialized software, providing a visual representation of the subsurface geology.
Drilling holes for kitchen cabinets can be tricky, requiring precise measurements. To ensure your design is perfect before you even pick up a drill, check out the best AI home design software for creating custom kitchen designs to plan everything out. This way, your drilling will be accurate and efficient, resulting in a beautifully installed kitchen.
These models are critical for various applications, including resource estimation, groundwater management, and hazard assessment. For example, data from multiple boreholes might reveal the extent of an ore body, allowing for more accurate estimations of resource potential.
Types of Samples Collected and Their Analysis
Geological drilling yields various types of samples, each providing unique insights into the subsurface. Core samples, as mentioned earlier, provide continuous records of rock formations. Cuttings, smaller rock fragments produced during drilling, are also collected and analyzed, offering information about the overall lithology. Fluid samples from boreholes can provide information on groundwater chemistry and potential contamination. Geophysical logs measure properties like density, porosity, and electrical conductivity, providing indirect but valuable information about the subsurface.
Laboratory analyses of these samples include petrographic analysis (microscopic examination of rocks), geochemical analysis (determination of chemical composition), and geotechnical testing (assessment of engineering properties).
Drilling, whether it’s for oil exploration or creating precise holes in a workpiece, requires accuracy. This precision is also crucial in home design, and understanding its limitations is key. Check out this article on exploring the limitations of using AI for home design online to see how AI struggles with the nuanced details. Ultimately, both drilling and successful home design rely on careful planning and execution for optimal results.
Geological Drilling Project Planning and Execution
The planning and execution of a geological drilling project involves several sequential steps. A flowchart illustrating this process would begin with Project Definition, encompassing defining objectives, selecting a location, and determining the required depth. This would be followed by Site Preparation, including obtaining permits and conducting site surveys. Next, Drilling Operations would involve setting up the drilling rig, conducting the drilling, and logging the borehole.
Sample Collection and Analysis would then occur, followed by Data Interpretation and Reporting, which includes analyzing the data and creating geological models. Finally, the project concludes with Site Restoration and Closure, encompassing the safe removal of equipment and restoration of the site to its original condition. This structured approach ensures a safe and efficient drilling operation, leading to the collection of high-quality data for geological interpretation.
Drilling Technology and Innovations
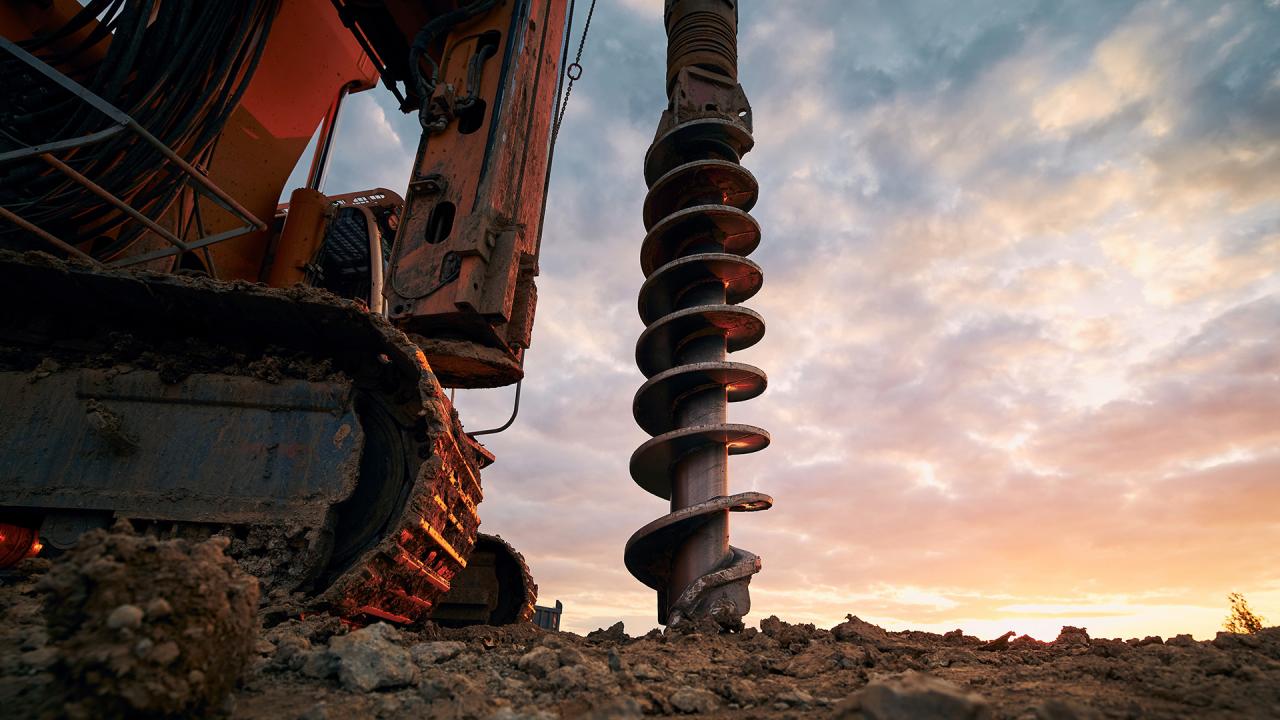
Source: com.au
The drilling industry, across its diverse sectors, has witnessed a remarkable evolution in technology, driven by the need for increased efficiency, reduced environmental impact, and enhanced safety. These advancements have significantly impacted drilling operations, from the initial planning stages to post-drilling analysis. This section explores some key technological innovations and their impact.Advancements in drilling technology have significantly improved efficiency and safety by enabling faster drilling rates, reducing non-productive time, and minimizing the risk of accidents.
For example, the development of more robust drilling bits and improved drilling fluids has allowed for deeper and more challenging wells to be drilled successfully. Simultaneously, real-time monitoring systems and advanced automation have enhanced safety protocols and minimized human error.
Automated Drilling Techniques
Traditional drilling methods relied heavily on manual operation and human judgment. Operators directly controlled the drilling parameters, relying on experience and intuition. Modern automated drilling techniques, however, leverage advanced sensors, sophisticated control systems, and real-time data analysis to optimize the drilling process. This automation allows for precise control of drilling parameters, leading to improved drilling performance and reduced downtime.
For instance, automated systems can adjust the weight on bit and rotary speed in real-time to optimize penetration rate and minimize vibrations, resulting in faster drilling and reduced wear on equipment. In contrast to the manual approach, where operator fatigue could lead to inconsistencies, automated systems maintain consistent performance throughout the drilling operation.
Emerging Drilling Technologies and Their Potential Impact
Several emerging technologies hold the potential to revolutionize the drilling industry. One such technology is the use of nanomaterials in drilling fluids. These materials can enhance the performance of drilling fluids, improving lubricity, reducing friction, and increasing the efficiency of the drilling process. Another promising area is the development of more efficient and environmentally friendly drilling fluids, reducing the environmental impact of drilling operations.
Furthermore, advancements in robotics and artificial intelligence are being explored for tasks like autonomous drilling and well inspection, promising greater safety and efficiency. For example, the use of remotely operated vehicles (ROVs) for subsea well intervention is already reducing the risks associated with working in hazardous underwater environments.
Data Analytics and Machine Learning in Drilling Operations
Data analytics and machine learning are transforming drilling operations by providing valuable insights into the drilling process. Sensors embedded in drilling equipment collect vast amounts of data, which can be analyzed to optimize drilling parameters, predict potential problems, and improve decision-making. Machine learning algorithms can identify patterns and trends in the data that may not be apparent to human operators, enabling proactive interventions to prevent costly downtime and optimize drilling performance.
For example, machine learning models can predict the risk of wellbore instability, allowing operators to take preventative measures before problems arise. This proactive approach reduces non-productive time and improves overall efficiency. The analysis of historical drilling data, combined with real-time data, allows for continuous improvement in drilling practices, resulting in safer and more efficient operations.
Environmental Impact of Drilling
Drilling operations, while crucial for various industries, have significant potential environmental consequences. These impacts can be widespread, affecting air, water, and land, and vary depending on the location, type of drilling, and implemented mitigation strategies. Understanding these impacts and implementing effective mitigation measures is crucial for responsible resource extraction and construction.
Potential Environmental Impacts of Drilling
Drilling activities can lead to a range of environmental problems. Air pollution from emissions of methane, a potent greenhouse gas, and other pollutants is a major concern. Water contamination from drilling fluids, produced water (brine), and spills can harm aquatic ecosystems and groundwater supplies. Habitat destruction and disruption due to land clearing and infrastructure development are also significant impacts.
Noise pollution from drilling equipment can disturb wildlife and nearby communities. Finally, the disposal of drilling waste presents challenges in terms of land use and potential contamination. The magnitude of these impacts depends on several factors, including the scale of the operation, the specific location, and the effectiveness of environmental management practices. For example, offshore drilling carries a higher risk of oil spills with potentially devastating consequences for marine ecosystems, as seen in the Deepwater Horizon disaster in the Gulf of Mexico.
Mitigation Measures for Environmental Impact
Numerous strategies are employed to lessen the environmental footprint of drilling. These include using environmentally friendly drilling fluids, implementing robust spill prevention and response plans, employing advanced waste management techniques, and implementing rigorous monitoring programs to detect and address potential environmental problems. Remediation efforts, such as restoring damaged habitats and cleaning up contaminated sites, are also crucial. Technological advancements, such as improved wellbore sealing techniques and the use of closed-loop drilling systems, aim to minimize the release of pollutants into the environment.
For instance, the use of biodegradable drilling fluids reduces the potential for water contamination. Careful site selection, minimizing land disturbance, and habitat restoration plans are also important components of effective mitigation strategies. The effectiveness of these measures is often evaluated through environmental impact assessments (EIAs) conducted before drilling commences.
Regulations and Guidelines for Environmental Protection
Numerous national and international regulations and guidelines govern drilling operations to protect the environment. These regulations often specify limits on emissions, waste disposal practices, and the use of certain chemicals. Enforcement agencies monitor compliance with these regulations, and penalties are imposed for violations. Specific regulations vary by location and the type of drilling activity. For example, offshore drilling is subject to stricter regulations due to the potential for large-scale spills and damage to marine ecosystems.
These regulations frequently require detailed environmental impact assessments (EIAs) before drilling projects can begin. The aim is to ensure that the potential environmental impacts are carefully considered and mitigated to an acceptable level. Compliance with these regulations is crucial for obtaining and maintaining operating permits.
Best Practices for Minimizing Environmental Footprint
Minimizing the environmental impact of drilling projects requires a proactive approach. This includes careful planning and site selection to avoid sensitive ecosystems. Employing advanced drilling technologies that minimize waste generation and emissions is crucial. Effective waste management practices, including recycling and proper disposal, are also vital. Regular environmental monitoring allows for early detection and mitigation of any potential problems.
Community engagement and transparent communication about project activities are essential for building trust and addressing concerns. Furthermore, continuous improvement through the adoption of best practices and technological advancements is essential for reducing the environmental footprint of drilling operations in the long term. Investing in research and development of cleaner drilling technologies remains a critical aspect of responsible drilling practices.
Wrap-Up: Drilling
From the vast oil fields to the operating room, drilling plays a crucial role in shaping our world. We’ve journeyed through the diverse applications of drilling, from the powerful machinery used in resource extraction to the delicate instruments employed in minimally invasive surgery. The challenges and innovations within this field are constantly evolving, driven by the need for increased efficiency, safety, and environmental responsibility.
Understanding the various aspects of drilling – its techniques, its impact, and its future – is crucial for appreciating its significance in modern society and for driving responsible advancements in this vital field.
FAQ Overview
What are the common causes of drilling accidents?
Common causes include equipment malfunction, human error (lack of training, fatigue, improper safety procedures), inadequate site preparation, and unforeseen geological conditions.
How is the depth of a drill hole measured?
Depth is typically measured using a depth gauge integrated into the drilling rig, which tracks the length of cable or drill string deployed.
What are the career opportunities in the drilling industry?
Opportunities range from rig operators and engineers to geologists, safety personnel, and project managers, spanning various skill levels and specializations.
What are some emerging trends in drilling technology?
Emerging trends include automation, robotics, advanced data analytics (AI/ML for optimization), and the development of more sustainable drilling fluids.
How does drilling contribute to climate change?
Drilling for fossil fuels contributes to greenhouse gas emissions, while drilling for geothermal energy can be a more sustainable alternative.